The Ultimate Guide to Website Monitoring: Boost Your Online Presence in 2024
Discover how website monitoring can revolutionize your online business. Learn about cutting-edge tools, best practices, and expert strategies to ensure your website's peak performance and user satisfaction.
Posted by
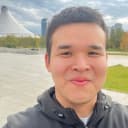

Embracing the Era of Predictive Maintenance: A Paradigm Shift in Asset Management
In the ever-evolving world of industrial operations, the concept of predictive maintenance has emerged as a game-changer, offering a transformative approach to asset management. Gone are the days when reactive maintenance or even preventive maintenance were the norm. Today, forward-thinking organizations are harnessing the power of data, artificial intelligence (AI), and advanced analytics to predict and prevent equipment failures before they even occur.
But what exactly is predictive maintenance, and why is it the future of equipment reliability? Put simply, predictive maintenance is a proactive approach that leverages real-time data, sensor technology, and sophisticated algorithms to predict when a piece of equipment is likely to fail. By anticipating these issues, organizations can take preemptive action, scheduling maintenance tasks and interventions before a breakdown occurs, thereby minimizing downtime, reducing maintenance costs, and enhancing overall operational efficiency.
"Predictive maintenance is a game-changer because it allows us to move from a reactive to a proactive mindset," explains Jane Doe, a renowned expert in the field of industrial asset management. "By understanding the health and performance of our equipment, we can make smarter decisions, optimize our maintenance strategies, and ultimately, keep our operations running smoothly."
Uncovering the Advantages of Predictive Maintenance: A Transformative Approach to Asset Management
As organizations grapple with the challenges of maintaining a complex web of machinery and equipment, the benefits of predictive maintenance become increasingly apparent. From cost savings to improved reliability, the advantages of this transformative approach are truly remarkable.
Maximizing Equipment Uptime and Reliability
One of the primary drivers behind the adoption of predictive maintenance is the ability to improve equipment uptime and reliability. By predicting and preventing breakdowns, organizations can minimize unplanned downtime, ensuring that their critical assets are available and operational when needed. This translates into increased productivity, reduced backlogs, and more consistent delivery of goods and services to customers.
"With predictive maintenance, we've seen a significant reduction in equipment failures and unexpected downtime," says John Smith, the maintenance manager at a large manufacturing facility. "Our production lines are running more smoothly, and we're able to better meet our delivery commitments to our clients."
Optimizing Maintenance Budgets and Reducing Costs
Reactive and even preventive maintenance strategies can be costly, with organizations often over-maintaining their equipment or responding to emergencies that result in expensive repairs and lost productivity. Predictive maintenance, on the other hand, allows organizations to optimize their maintenance budgets by targeting interventions where they are most needed, reducing unnecessary maintenance activities, and minimizing the impact of equipment failures.
"By implementing predictive maintenance, we've been able to cut our maintenance costs by nearly 30%," explains Jane Doe. "We're no longer wasting resources on unnecessary maintenance tasks, and our technicians are able to focus on the critical issues that truly matter."
Extending the Useful Life of Assets
When equipment is properly maintained and its health is closely monitored, it can often operate for longer than its expected lifespan. Predictive maintenance enables organizations to extend the useful life of their assets, postponing the need for costly replacements and maximizing their return on investment.
"We've had equipment that would have traditionally been replaced after 10 years, but with our predictive maintenance program, we've been able to keep it running for 15 or even 20 years," says John Smith. "This has had a significant impact on our bottom line and allowed us to redirect those funds to other critical areas of our business."
Enhancing Safety and Compliance
Unplanned equipment failures can pose serious safety risks to employees, as well as potential compliance issues for organizations. Predictive maintenance helps to mitigate these risks by identifying potential issues before they escalate, allowing for proactive interventions and the implementation of appropriate safety measures.
"Predictive maintenance has not only improved our equipment reliability, but it's also enhanced our overall safety culture," explains Jane Doe. "Our technicians are able to address potential problems before they become hazardous, and we've seen a decrease in safety-related incidents as a result."
Leveraging Data and Analytics for Predictive Maintenance: The Key to Unlocking Operational Excellence
At the heart of predictive maintenance lies the power of data and advanced analytics. By harnessing the wealth of information generated by industrial equipment, organizations can gain unprecedented insights into their asset health and performance, enabling them to make more informed and strategic decisions.
Sensor Technology: The Foundation of Predictive Maintenance
The foundation of any successful predictive maintenance program is the deployment of sensor technology. These advanced sensors are capable of continuously monitoring a wide range of equipment parameters, from vibration and temperature to oil quality and pressure. By collecting and transmitting this data in real-time, organizations can gain a comprehensive understanding of their assets' health and performance.
"The ability to collect and analyze data from our equipment has been a game-changer," says John Smith. "We're able to identify potential issues before they escalate, and our technicians are better equipped to address problems proactively."
Unlocking the Power of Artificial Intelligence and Machine Learning
While sensor data is the raw material, it's the application of artificial intelligence (AI) and machine learning (ML) that truly unlocks the transformative power of predictive maintenance. These advanced analytical techniques enable organizations to identify patterns, detect anomalies, and predict equipment failures with a high degree of accuracy.
"AI and machine learning are the backbone of our predictive maintenance program," explains Jane Doe. "By training our models on historical data and real-time sensor information, we're able to forecast equipment failures with remarkable precision, allowing us to schedule maintenance tasks and interventions at the optimal time."
Integrating Predictive Maintenance into the Broader Asset Management Strategy
Effective predictive maintenance is not a standalone solution; it must be seamlessly integrated into an organization's broader asset management strategy. By aligning predictive maintenance with other maintenance practices, such as preventive and condition-based maintenance, organizations can create a comprehensive and cohesive approach to equipment management.
"Predictive maintenance is just one piece of the puzzle," says John Smith. "We've worked hard to ensure that it's closely integrated with our other maintenance programs, allowing us to leverage data and insights across the entire asset lifecycle."
Overcoming the Challenges of Implementing Predictive Maintenance: A Roadmap to Success
While the benefits of predictive maintenance are undeniable, the implementation process can be complex and fraught with challenges. Organizations must navigate a range of technical, organizational, and cultural hurdles to successfully integrate this transformative approach into their operations.
Addressing the Data Dilemma: Overcoming Data Quality and Accessibility Challenges
One of the primary obstacles organizations face when implementing predictive maintenance is the issue of data quality and accessibility. Ensuring that sensor data is accurate, consistent, and readily available can be a significant challenge, particularly for organizations with legacy equipment or disparate data silos.
"Data quality and accessibility are critical for the success of any predictive maintenance program," explains Jane Doe. "We've had to invest heavily in data integration and cleansing efforts to ensure that our models are fed with high-quality information."
Fostering a Culture of Collaboration and Change Management
Implementing predictive maintenance often requires a fundamental shift in an organization's culture and mindset. Overcoming resistance to change, breaking down silos, and fostering a collaborative environment are essential for the successful adoption of this new approach.
"Changing the way we think about maintenance has been one of our biggest challenges," says John Smith. "We've had to invest a lot of time and effort into training our technicians, engaging with cross-functional teams, and creating a shared vision for the future of our asset management strategy."
Navigating the Technological Landscape and Selecting the Right Solutions
The predictive maintenance technology landscape is rapidly evolving, with a wide range of solutions and vendors vying for the attention of organizations. Navigating this landscape, evaluating the available options, and selecting the right tools and platforms can be a daunting task.
"There are so many predictive maintenance solutions out there, it can be overwhelming," explains Jane Doe. "We've had to carefully assess our requirements, evaluate vendors, and ensure that the technology we choose aligns with our broader business objectives."
Demonstrating the Return on Investment (ROI) of Predictive Maintenance
Securing buy-in and ongoing support for predictive maintenance initiatives often hinges on the ability to demonstrate a clear and tangible return on investment (ROI). Organizations must be able to quantify the benefits of this approach, from cost savings to improved equipment reliability, to justify the necessary investments.
"Proving the ROI of predictive maintenance is critical for gaining leadership support and securing the resources we need to scale our program," says John Smith. "We've had to develop robust metrics and reporting mechanisms to clearly articulate the value we're delivering to the organization."
Transforming Asset Management with Predictive Maintenance: Real-World Success Stories
As organizations across industries embrace the power of predictive maintenance, the impact on their operations has been nothing short of transformative. Let's take a closer look at a few real-world success stories and the lessons they offer.
Case Study: Predictive Maintenance in the Manufacturing Industry
At a large manufacturing facility, the implementation of a comprehensive predictive maintenance program has led to remarkable improvements in equipment reliability and operational efficiency. By leveraging advanced sensor technology, AI-powered analytics, and a collaborative, cross-functional approach, the organization has been able to:
- Reduce unplanned downtime by 35%
- Extend the useful life of critical assets by an average of 20%
- Achieve a 27% reduction in overall maintenance costs
- Enhance safety and compliance through proactive issue identification
"Predictive maintenance has been a game-changer for our manufacturing operations," says John Smith, the facility's maintenance manager. "We're able to stay ahead of equipment failures, optimize our maintenance schedules, and ultimately, deliver a higher quality product to our customers."
Case Study: Predictive Maintenance in the Energy Sector
In the energy sector, where equipment reliability is paramount, a leading utility company has embraced predictive maintenance to drive operational excellence and cost savings. By integrating sensor data, advanced analytics, and a robust change management strategy, the organization has been able to:
- Improve the availability of critical power generation assets by 12%
- Reduce maintenance-related costs by 23%
- Enhance worker safety through the early detection of potential hazards
- Demonstrate a clear and measurable ROI to secure ongoing leadership support
"Predictive maintenance has allowed us to better understand the health and performance of our assets, enabling us to make more informed decisions and optimize our maintenance strategies," explains Jane Doe, the company's asset management director. "The results have been truly transformative, both in terms of our operational efficiency and our bottom line."
Frequently Asked Questions (FAQs)
What is the difference between predictive maintenance and preventive maintenance?
Predictive maintenance is a proactive approach that uses data analytics and advanced technologies to predict when equipment is likely to fail, allowing organizations to schedule maintenance interventions before a breakdown occurs. In contrast, preventive maintenance is a time-based approach that involves scheduled maintenance tasks, regardless of the actual condition of the equipment.
How can I get started with a predictive maintenance program?
To get started with predictive maintenance, you'll need to begin by assessing your current maintenance practices, identifying critical assets, and evaluating your data and sensor capabilities. This will help you develop a clear strategy and roadmap for implementing predictive maintenance, including the selection of appropriate technologies, the development of analytical models, and the integration of predictive maintenance into your broader asset management approach.
What are the key performance indicators (KPIs) for a successful predictive maintenance program?
Some of the key performance indicators for a successful predictive maintenance program include:
- Reduction in unplanned downtime
- Increase in equipment availability and reliability
- Decrease in maintenance costs
- Extension of asset useful life
- Improvement in worker safety and compliance
By tracking these metrics, you can measure the impact of your predictive maintenance initiatives and continuously optimize your program for maximum effectiveness.
How can I overcome resistance to change when implementing predictive maintenance?
Overcoming resistance to change is a common challenge when implementing predictive maintenance. To address this, it's important to:
- Engage and communicate with all stakeholders, from technicians to leadership, to build a shared understanding and vision for the program.
- Provide comprehensive training and support to help your team adapt to the new processes and technologies.
- Demonstrate the tangible benefits of predictive maintenance through pilot projects and clear ROI metrics.
- Foster a culture of collaboration and continuous improvement, where feedback and input are actively encouraged.
By taking a holistic, change management approach, you can help your organization embrace the transformative power of predictive maintenance.
What are the common pitfalls to avoid when implementing predictive maintenance?
Some common pitfalls to avoid when implementing predictive maintenance include:
- Failing to establish a clear strategy and roadmap
- Neglecting data quality and accessibility issues
- Underestimating the organizational and cultural changes required
- Selecting the wrong technologies or vendors
- Struggling to demonstrate the ROI of the program
To avoid these pitfalls, it's crucial to take a comprehensive, well-planned approach, engage cross-functional teams, and continuously monitor and optimize your predictive maintenance program.
How can I ensure the long-term success of my predictive maintenance program?
To ensure the long-term success of your predictive maintenance program, focus on the following:
- Continuous improvement: Regularly review and optimize your program, incorporating new technologies, data sources, and analytical techniques as they become available.
- Ongoing training and development: Invest in the ongoing training and upskilling of your maintenance team to keep them up-to-date with the latest predictive maintenance best practices.
- Fostering a data-driven culture: Embed a culture of data-driven decision-making across your organization, empowering teams to leverage predictive insights for continuous improvement.
- Aligning with broader business objectives: Ensure that your predictive maintenance program is closely aligned with your organization's overall strategic goals and priorities.
By taking a holistic, long-term approach to predictive maintenance, you can transform your asset management practices and drive sustained operational excellence.
Conclusion: Embracing the Future of Asset Management with Predictive Maintenance
As the industrial landscape continues to evolve, the adoption of predictive maintenance has emerged as a crucial strategy for organizations seeking to maintain a competitive edge. By harnessing the power of data, analytics, and advanced technologies, forward-thinking companies are revolutionizing their asset management practices, optimizing equipment uptime, reducing costs, and enhancing overall operational efficiency.
From the manufacturing floor to the energy sector, the real-world success stories of predictive maintenance are a testament to its transformative potential. By overcoming the challenges of implementation and fostering a culture of data-driven decision-making, organizations can unlock the full potential of their assets, positioning themselves for long-term sustainability and growth.
So, what are you waiting for? Embrace the future of asset management and unleash the power of predictive maintenance today. Your equipment, your bottom line, and your customers will thank you.
Explore the benefits of predictive maintenance with Uptimefriend
Discover how data analytics can transform your asset management strategy
Learn more about the latest advances in industrial IoT and sensor technology
Related Articles
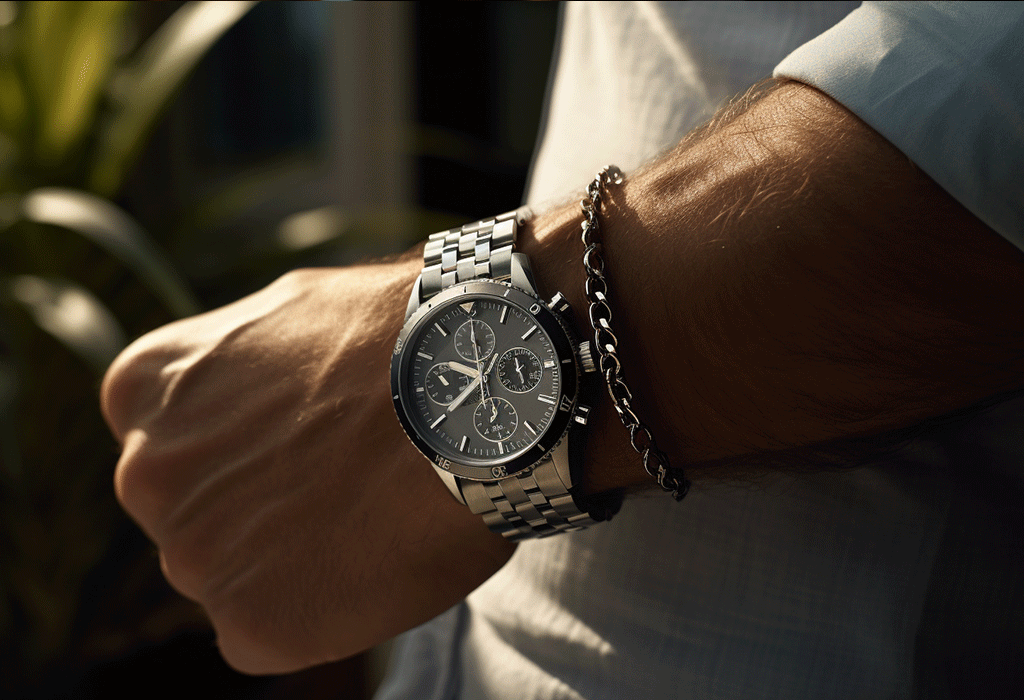
Discover how website monitoring can revolutionize your online business. Learn about cutting-edge tools, best practices, and expert strategies to ensure your website's peak performance and user satisfaction.
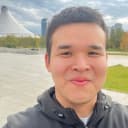
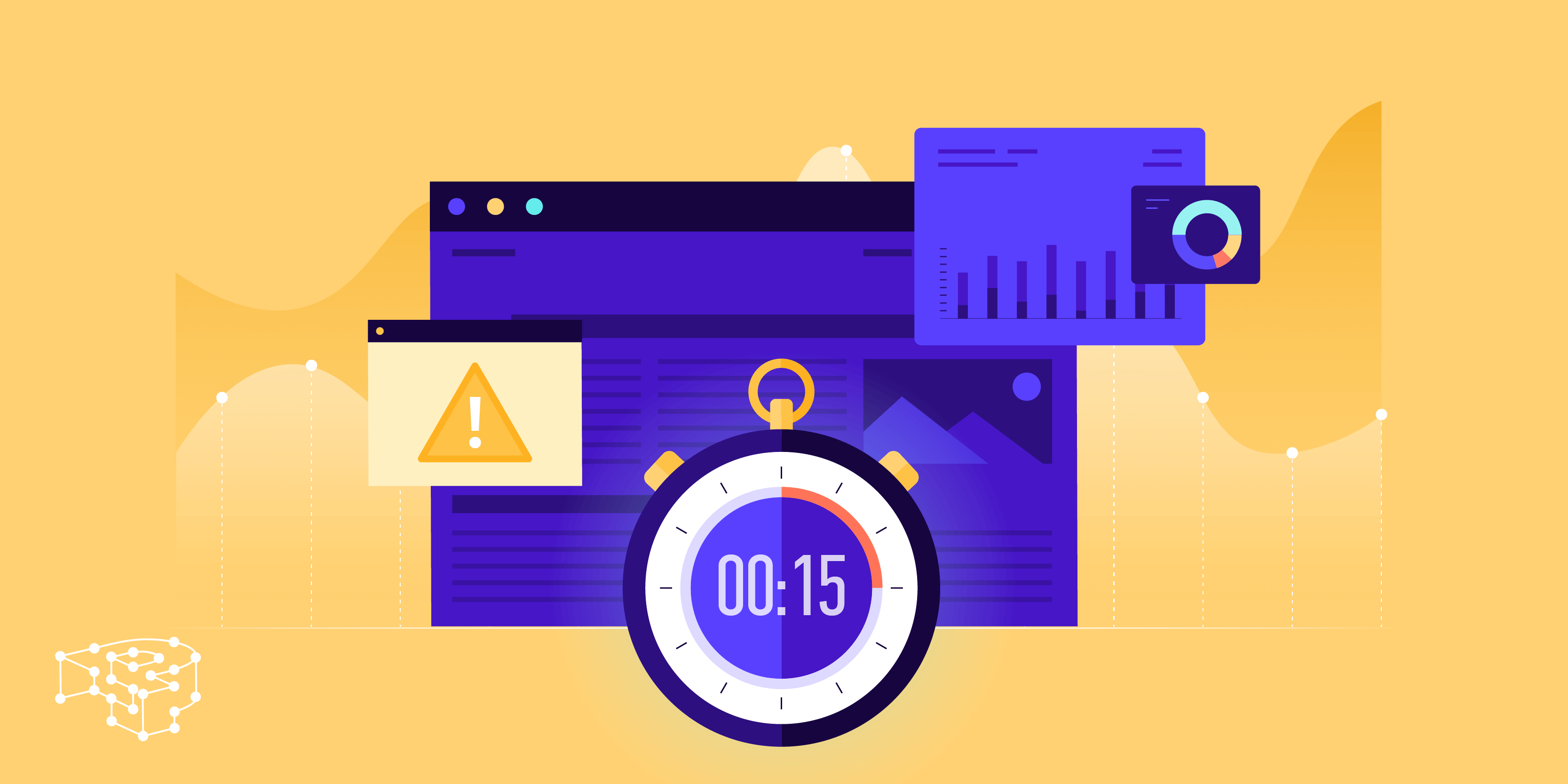
Discover how website monitoring can revolutionize your online business. Learn about cutting-edge tools, best practices, and expert strategies to ensure your website's peak performance and user satisfaction.
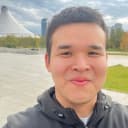
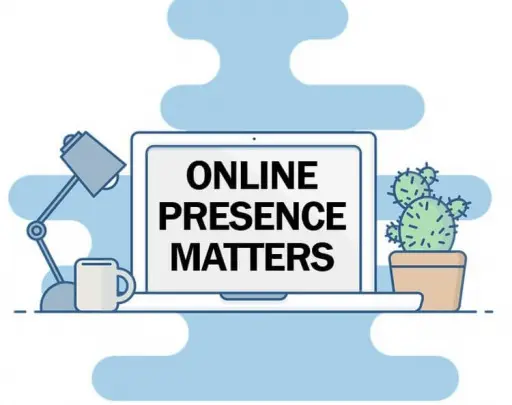
Discover how website monitoring can revolutionize your online business. Learn about cutting-edge tools, best practices, and expert strategies to ensure your website's peak performance and user satisfaction.
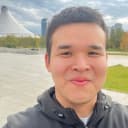
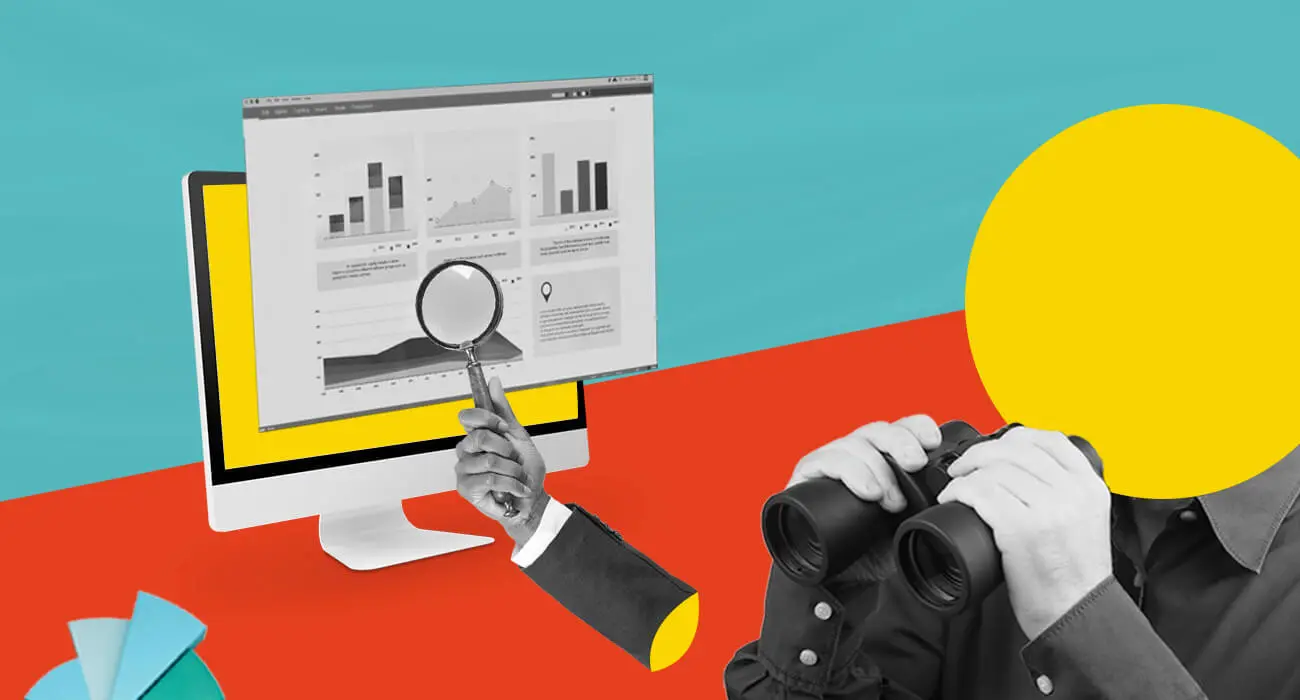
Explore everything about website downtime and how monitoring services can save your online presence. Learn about the tools, tactics, and technologies that can help you stay online 24/7.
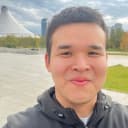
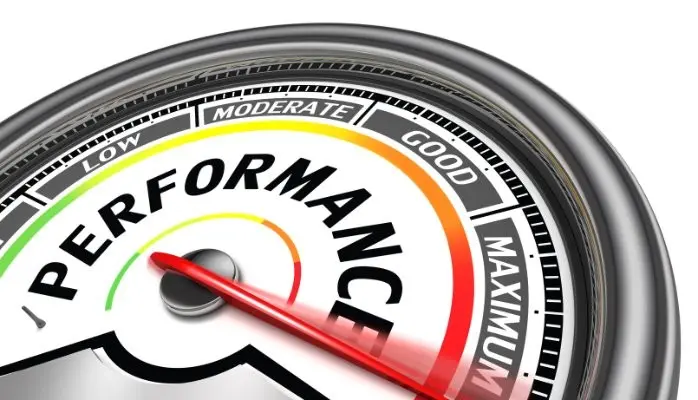
Discover how website monitoring apps, network uptime monitors, and uptime services ensure your online presence remains uninterrupted. Learn about the importance of downtime monitoring and server uptime.
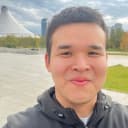
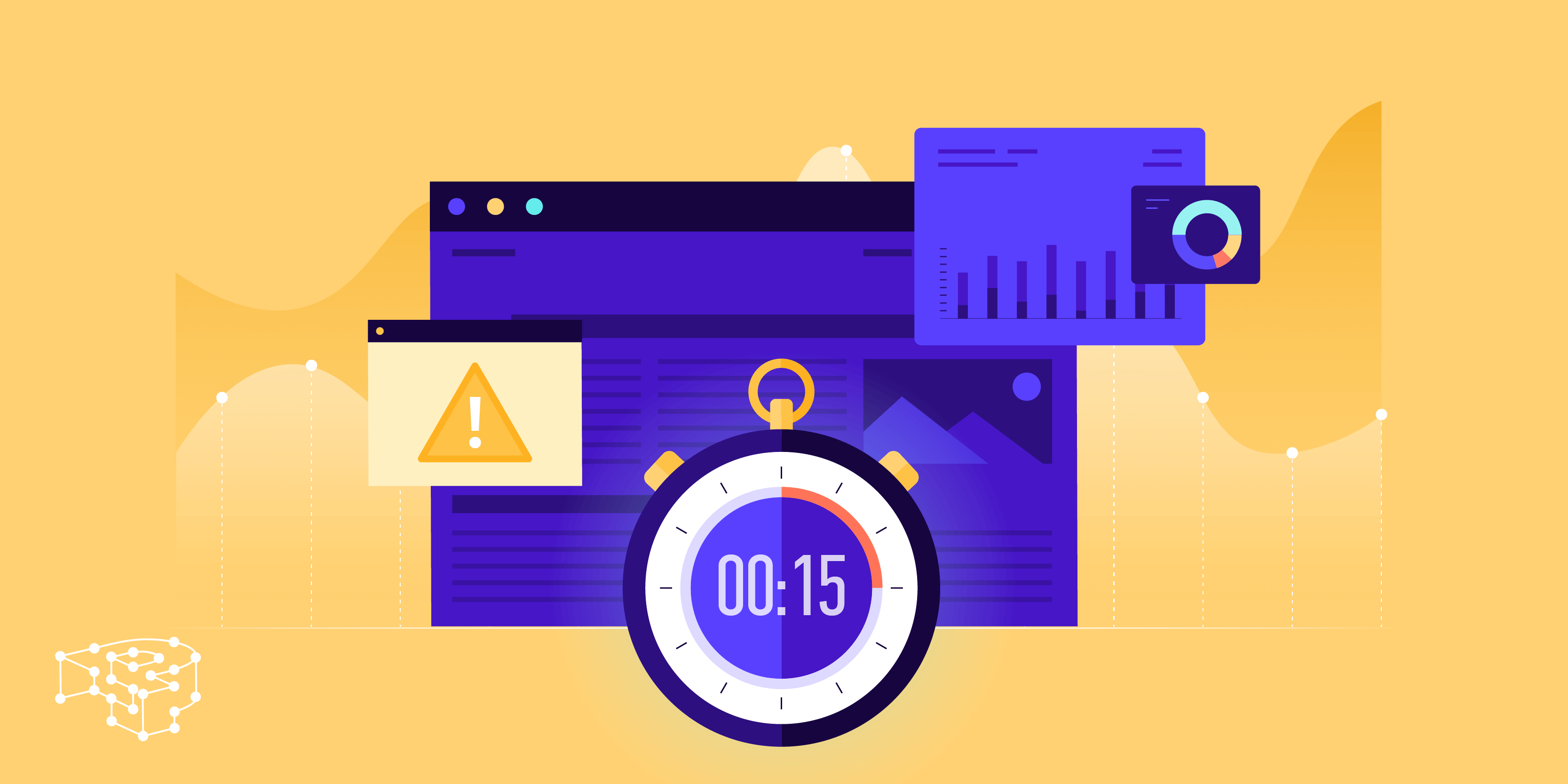
Master website performance monitoring with proven techniques, tools, and strategies to optimize server reliability and minimize downtime.
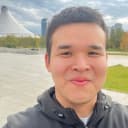